FAQs
Select one of the categories to find the desired
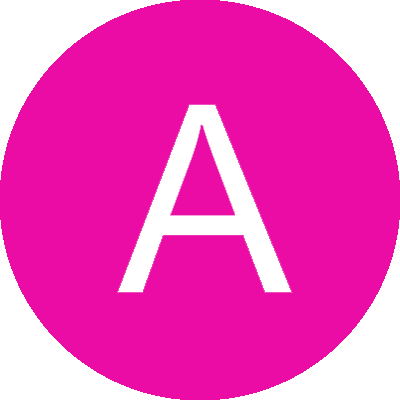
I. Problems:
The flour mill produces flour at too high a temperature
Solution:
Should be appropriate to loosen the clearance of the grinding rollers, such as the cause of wear and tear of the grinding rollers, should be repaired or replaced in time; summer should be especially pay attention to, pay attention to the heat dissipation of the flour mill.
II,
Problems: flour mill in the normal production of less powder or no powder
Solution: it is likely that the sieve mesh is blocked, clean up the sieve mesh or replace the new mesh.
Three,
Problems: the flour mill works normally, but the output has dropped
Solution: Adjust the gap between the grinding rollers, press the spring to ensure that the gap between the two ends of the grinding rollers is consistent. It is also possible that the grinding teeth are used for a long time, caused by serious wear and tear, and should be re-drawn.
Four,
Problems: wheat flour mill such as shaking phenomenon
Solution: The fixing screws should be checked and the coupling bolts between the mill head and the frame should be tightened. Check the solid condition with the ground angle screws.
Five,
Problems: flour mill only out of flour, not out of bran
Solution: The common reasons are the main shaft steering is not right, the sieve mesh is broken or the sieve frame is not sealed tightly.
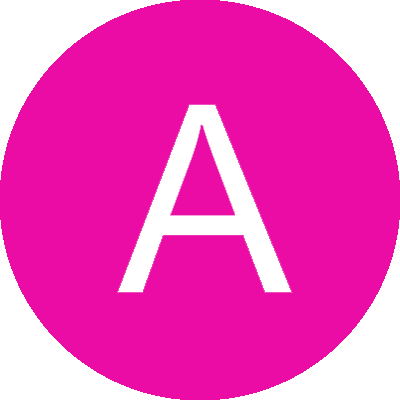
What are the methods of unloader inspection and maintenance? The layout of the unloader is careful, long application life, but the unloader in some cases of improper device or material is not suitable will form the unloader motor fault, then the formation of motor fault causes and how to prepare for it is necessary to understand, so that later you can prevent the reappearance of similar failures.
(1) unloader check the surrounding environment will affect the motor heat dissipation consequences of the formation of motor destruction
(2) unloader selection is not right the amount of material unloaded is too large, greater than its own unloading capacity, long time overload things to extend the application of the life of the motor
(3) the viscosity of the material unloaded by the unloader is too high motor pressure is too large to form a destruction
(4) unloader motor wiring is solid. The above four situations are prone to form the unloader motor dust fault, affecting the normal things of the unloader, so customers must pay attention to the application or device purchasing.
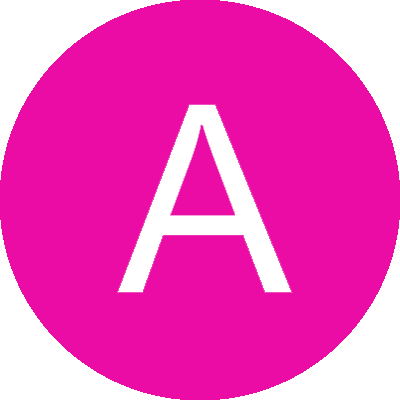
1. Do maintenance work every day, start and shut down the machine, check, there is no damage to the equipment.
2. Regularly on the unloader above the dust, to carry out a clear gray work.
3. Regular replacement, regular inspection, good ventilation.
4. unloader speed, as far as possible, do not so fast, do not let him overloaded.
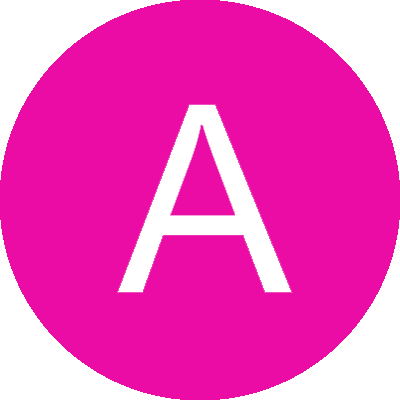
Pulse bag filter because of improper installation or operation may lead to damage to the filter bag, then we analyzed according to the actual situation of the project. Found that in half a year of operation in the filter bag damage is more, but also because of the resulting emission concentration does not meet the standard, then the unit after several downtime maintenance on the filter bag damage causes were analyzed.
1、 Filtration wind speed
In the dust collector design, if the excessive pursuit of small size, low cost is to choose too high a filtration wind speed, easy to cause the operating resistance to increase the frequency of clearing, thus greatly shortening the service life of the filter bag. Dust collector does not clear the dust when the filter wind speed selection 0.66 m/min, wind speed in a reasonable range is also to avoid the filter wind speed is too high will cause adverse effects on the filter bag.
2、Temperature influence
The service life of different filter bag materials are different, the overall service life of the filter bag material in the coating treatment is not less than 3 years, and the normal permissible flue gas operating temperature is within 100 ~ 130 ℃, and even said that the instantaneous temperature allowed by the pulse bag filter can reach 180 ℃. When the operating temperature is too high, the actual exhaust temperature is controlled at about 160℃, not exceeding the peak instantaneous temperature and continuous operation temperature of PTFE, avoiding the filter bag being burnt in a short time because of the high temperature of the flue gas. At the same time, the exhaust temperature is too low, water vapor in the flue gas condensation through the filter bag attached to the filter bag will also cause the filter bag plate.
3、 Blowing wear
When the blowing pressure is too high, it will increase the impact of the soot cleaning airflow on the filter bag, resulting in scouring wear; blowing time interval is set unreasonably frequently blowing; blowing compressed air quality is not qualified with water with oil so long time will cause the filter bag slate.
4、 Oil adhesion
Due to frequent boiler ignition start and low load operation, need to throw oil for a long time, then there will be unburned oil adhering to the filter bag, so that the filter bag gradually lose activity, thus causing serious damage.
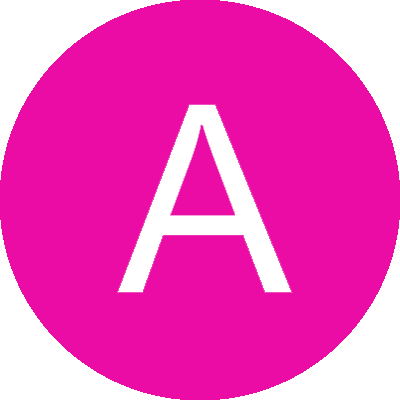
Must look at his function unloader is divided into many kinds of models are not the same, some are high temperature resistance, some are wear-resistant, must look at this standard, can not buy wrong. Poor performance must not unloader is also divided into a lot of performance, poor performance must not, the performance of the unloader is very important, the performance of the product is not good, there may be a decline in the overall performance, and sometimes also and other equipment does not match. First look at their own manufacturers, in the selection of unloader whether you buy a dust collector or unloader, you should first look at their own manufacturers to see what model of unloader is suitable for, in making a decision, which is very important.
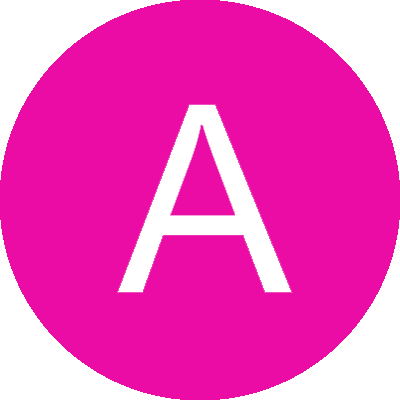
Most of the flour we usually see, this is because the flour machine in the flour production and processing, but also through the drying process. Flour machine to flour drying is not in place or drying excessive will have bad results:
First of all, flour machinery in the processing of flour before, are to put the wheat in the water to wash a wash, this is in order to flour clean needs, of course, this is a large flour machine assembly line operation, not a separate process. After washing, the wheat is easy to take off the seed coat, and the wheat kernel is processed into flour, which is the role of moisture, and in the process, there is no drying of the wheat kernel, so the processed flour is wet.
If the flour is too dry, there will be a lot of flour flying into the air, when the air reaches a certain concentration of flour, if there is an open flame flash, there will be an explosion, the consequences of the flour explosion, and the gas is no different from the power, it does not matter that the explosion is generated.
However, this is only due to the flour milling process, will not have any effect on the quality of the flour, so please feel free to buy and use.

HOW CAN WE HELP ?
Get In Touch With Us!
Contact Information
Fax: +86-371-23227333
E-mail: global@aomgmach.com
Production base: Zongdian Industrial Zone, Qi County, Kaifeng City